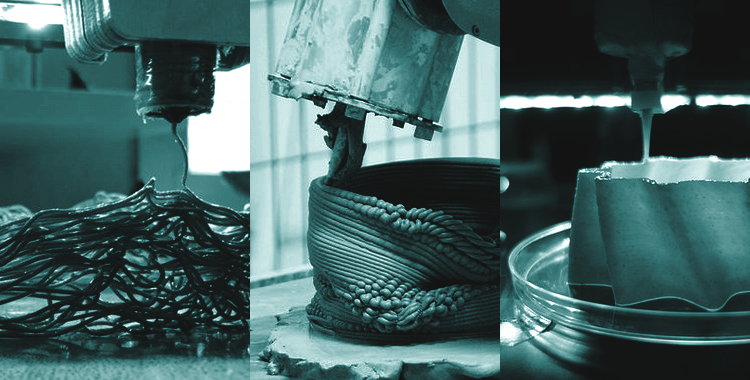
inFORMed matter – research project
The “inFORMed matter” research project focuses on the exploration of additive fabrication processes (such as n-Dimensional printing, guided growth and/or assembly), aiming to inform (i.e. to give form) as in to produce form through the morphogenetic properties and capacities of matter by embedding further information structures during the fabrication process itself by means of mechanical (robots, printers, etc.) and/or biological (organisms – even synthetically built ones) constructor agents.
Our goal is to go beyond the current state of prototyping, according to which the physical prototype should be as close as possible to a clone of its digital counterpart, thus making fabrication a purely replicational phase. Instead, by coding and embedding additional levels of information aimed at mapping and/or defining material features and behaviors as well as different deployment patterns from which physical and aesthetic properties arise, the production and digital fabrication phase becomes an integral part of the design process.
By exploring the code-matter-machine (whether mechanical or biological) interaction process we can study the potential emergent behaviors of the system as well as learn and exert a new sensibility to the computational design/fabrication process by tapping into the self-organization properties of matter as a key factor in determining characteristics of the output shape.
The research is articulated in 4 main points:
- anticipate material behavior through digital simulation: test and apply different tool-based conditions and parameters (extrusion direction angle, speed of extrusion, variable layer thickness, etc … ) and evaluate the consequent material behavior in order to get useful feedback for the next iteration of the digital model. The aim is to understand how to embed material properties as code/information during the digital design phase, fine tuning it towards the desired effect-outcome
- Seamless design-to-machine pipeline: shorten the information pipeline from the design process to the constructor machine. This is achieved by acting on both factors: informing directly the machines by generating the necessary code in the design tool and build the design process around the capacities of the machines involved.
- Embed morphogenetic material properties as design factors: understand and manage such properties, behaviors and their potential morphological outcomes for different materials, from clay to biologic matter, in order to map and use them as an atlas of expressive possibilities and performances of the material.
- Understand constraints and opportunities determined by the chosen constructor agent/machine: learn to use and manage different machines to handle the extrusion tool for additive processes and learn to evaluate and exploit the influence, constraints and given opportunities provided by different machines and movement technologies.
The final output is then the result of influence, cooperation and conflict of these aspects upon, with and onto one another. Only successfully combining computational simulation, material properties and capacities and machine constraints and opportunities we can effectively evaluate and push further the design process potential and foster design and fabrication skills and sensibilities that will form the basis of a more comprehensive awareness in regard to the relations between computation and material aspects.
The Co-de-iT team is currently declining such research through various explorations:
. inFORMed CLAY matter
https://flic.kr/s/aHskQLzGvn
https://flic.kr/s/aHsk5Uuipc
. Bio-Ex Machina (formerly Bio-Logic)
https://flic.kr/s/aHskRXxFES
https://www.co-de-it.com/wordpress/nexto-biologic-workshop-report.html
https://www.flickr.com/photos/co-de-it/sets/72157640140974623
. P5 + experimental 3D printing
https://www.co-de-it.com/wordpress/p5experimental-3d-printing.html
[…] [.] Brief: The workshop idea rises from a collaboration between Co-de-iT, Fablab Torino, Officine Arduino, based on an ongoing Co-de-iT research called “inFORMed matter“. […]
[…] during the “Experimental Materiality Day” on 17th Sept. 2015. We will talk about our inFORMed matter research and the digifabTURINg collaboration experience and research. We will exhibit also some 3d printed […]
[…] Project developed under the workshop inFORMed Clay Matter 2.0, under the tutorship of Andrea Graziano, by Co-de-iT, Fablab Torino, Officine Arduino, based on an ongoing Co-de-iT research called “inFORMed matter“. […]